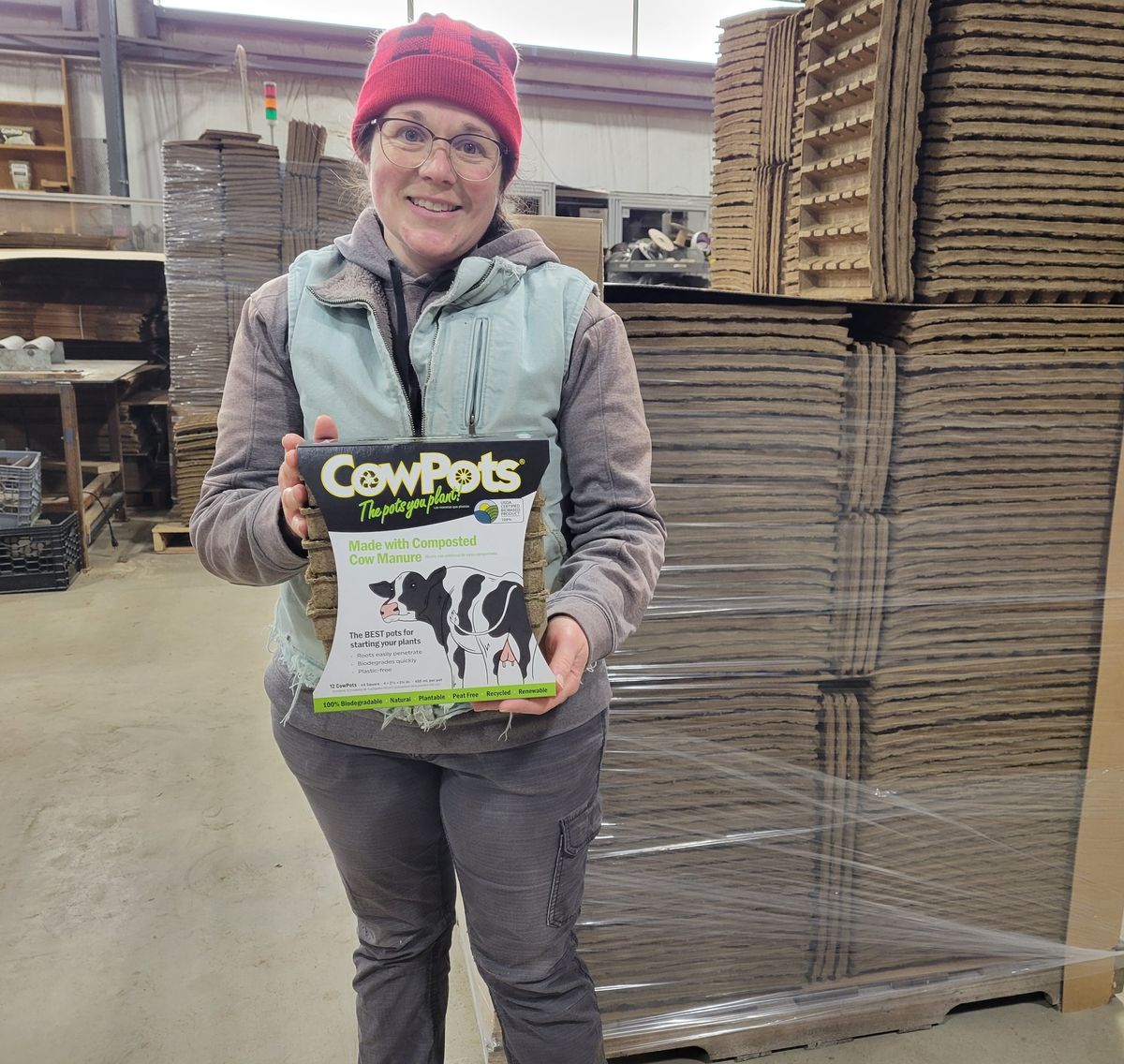
Amanda Freund oversees the CowPots manufacturing operation at her family’s farm in East Canaan. Stacked behind her is a pallet of the company’s newest product: seed starter trays.
Debra A. Aleksinas
Amanda Freund oversees the CowPots manufacturing operation at her family’s farm in East Canaan. Stacked behind her is a pallet of the company’s newest product: seed starter trays.
NORTH CANAAN — By producing 2 billion disposable plastic syringes a year, BD’s (Becton Dickinson and Company) North Canaan plant has the potential to touch a quarter of the world’s population.
“And that’s just out of this one factory alone,” said Dustin Andersen, plant director of the 400,000-square-foot manufacturing plant on Grace Way off rural Route 63.
“I tell all the new hires when they come in, we make 6 million syringes a day, which means every person in the state of Connecticut could come into this factory, we could give them a syringe every day, and still have millions left over to distribute,” noted Andersen, who oversees operations at the 60-year-old facility, which spans 10 acres under one roof.
“When you’re working for a company that has that kind of impact, it really stands for something.”
BD is one of a handful of manufacturers in the state’s bucolic Northwest Corner making a significant impact locally and globally by stimulating the economy, providing jobs for the community, launching innovative technology and embracing renewable resources.
In addition to BD, a handful of other major manufacturers in the Northwest Corner with a global scope include:
— The Lakeville-based ITW (Illinois Tool Works) Seats & Motion Division within the ITW Automotive Segment, which molds and assembles 45 million headrest guides per year for Ford and Toyota vehicles throughout North America and Venezuela.
— CowPots, one of three businesses owned and operated by the multigenerational Freund family farm in East Canaan, where tens of millions of eco-friendly flowerpots made from composted manure have been manufactured over the past 27 years using the longest continuously operating methane digester in the country.
— Hutzler Manufacturing, a four-generation family-owned and -operated business in North Canaan that has been designing and producing housewares since 1938, including innovative utensils for several popular fast-food giants.
“Rural manufacturers are a critical piece of Connecticut’s overall economy and their products impact lives around the world,” said Chris DiPentima, resident and CEO of the Connecticut Business and Industry Association (CBIA).
They are also “critical to local economic development, supporting and revitalizing local communities not only through the hundreds of millions in state and local taxes that they pay, but also because they create five additional jobs in other parts of the state’s economy for every one manufacturing job, and generate $2.60 in additional economic activity for every $1 spent in manufacturing.”
Those are huge multipliers, said DiPentima, “equivalent to what Silicon Valley experienced with the tech-sector boom — and high wage careers with the average Connecticut manufacturing salary at $92,633, 36% higher than the national average and 14% more than the state’s average salary.”
Courtesy of BD
Dustin Andersen is the plant director at BD Canaan, which is the largest employer in the Northwest Corner, with more than 400 employees.
Innovation transformed BD
The first wave of disposable plastic syringes were manufactured out of BD’s North Canaan facility in 1961 in its original 25,000-square-foot-building, manned by eight associates. The innovation soon transformed BD by replacing traditional glass syringes to ensure more sterile conditions.
“The PlastiPak syringe was really what put us on the map,” said Andersen.
One year later, BD purchased a 77-acre tract of land and broke ground for the construction of a 55,000-square-foot state-of-the-art plant, and since then, has expanded the North Canaan facility eight times, for a total of 360,000 square feet.
Until you’ve toured the plant, it’s difficult to comprehend the scale of the operation.
The operation is a vital facility for the BD Medical -Medical Surgical Systems unit of its parent, Becton Dickinson and Company, which was founded in 1897 and is headquartered in Franklin Lakes, New Jersey.
About 400 employees work at the North Canaan facility, making it the largest employer and taxpayer in the Northwest Corner.
“Everybody around here knows somebody who is working at BD,” Andersen explained.
Jeanine Hodgekiss, BD’s customer complaint and validation quality manager and a second-generation associate, noted that the “quality” within the facility extends far beyond the products produced.
“I’ve been at BD for 34 years, and my dad worked there over 30 years,” said Hodgekiss “When people think of quality, they think of the product. But BD also provides the quality of life.”
Steve Furth is the plant manager at ITW Seats & Motion Division in Lakeville, which manufactures automobile headrest guides for Ford and Toyota. Debra A. Aleksinas
Building a ‘model factory’ in Lakeville
The odds are that anyone who owns a Toyota Tacoma pickup truck is driving around with a plastic component tucked into the vehicle’s headrest that was molded by ITW’s Seats & Motion Division in Lakeville. Ditto for Ford vehicles on the road today.
The global operation takes place in a commercial building adjacent to the Lakeville Hose Company, where plastic headrest guides, a key safety component in automobiles, are produced by 38 molding and 15 assembly machines in the 20,000-square-foot plant.
“We make them for 98% of the Fords that are built in North America,” said Steve Furth, the operation’s plant manager, during a recent tour of the totally automated facility.
“Toyota is getting close to Ford” in terms of production, said Furth as he pointed out the five molding machines and three assembly machines pumping out and assembling headrest guides for Tacoma vehicles. “We ship 100,000 parts a week.”
As he spoke, the machines whirred as they completed various steps of the process, work that up until about three years ago, was done primarily through manual labor.
To keep up with the volume, for several years, ITW rented warehouse space in Millerton, New York, for storage, packing and shipping. Now, the entire process takes place in Lakeville.
“Three years ago, the company decided it was time to do what we call ‘model factory,’” said Furth, which improved efficiency through automation but resulted in the closing of the Millerton site and downsizing the workforce from 50 to about 35.
“It did take some jobs away, but it improved our efficiency tenfold. We now produce about 45 million parts per year.”
Furth, who has been employed by ITW for 15 years, marveled that even though ITW global has 35 locations worldwide with an estimated 28,000 employees, that a modest plant in rural Lakeville is part of that world-wide success.
“How this little factory got started in this area up here, nobody knows, but here we are.
”‘Dirty Jobs,’ the pandemic, fueled CowPots
Tucked away on a winding dirt road behind the Freund family farm’s dairy operation and farm market and bakery, is a manufacturing plant that molds eco-friendly flowerpots made from composted manure.
On a recent visit to the operation, Amanda Freund, third generation of the family farm, manages the CowPots operation with her father, Matt Freund. The second-generation Freund, with help from a friend with an engineering background, designed the technology used to mold dried manure into flower pots as an alternative to peat pots, which take longer to biodegrade.
Diversification, said Amanda Freund, was a saving grace when the pandemic hit in 2020. The family’s 300-cow dairy operation was in ”crisis mode,” she recalled, as demand for milk dried up when schools, restaurants and other customers closed shop.
But at the same time, “everyone was home, and gardening blew up,” and demand for CowPots skyrocketed.
In 2007, CowPots gained “incredible national exposure” when it was featured not only on “Larry King Live,” but also in a segment of “Dirty Jobs” with Mike Rowe.
“It was incredible national exposure, with reruns in 125 countries to this day, which I can always track by the spike in visits to my website,” Freund noted.
The CowPots operation maintains a health permit with the USDA to be able to export product to the European Union, and Freund said she is two to three years into a discussion with a company in Australia “that has begun the process of licensing our technology and some form of royalties.”
“With 500 million tons of plastic per year produced from the horticultural industry,” she said, “we’re pushing to be part of the solution.”
An engineering breakthrough
Also on Grace Way in North Canaan, across from BD, is the Hutzler Manufacturing Company Inc., a four-generation, family-owned and -operated manufacturer and worldwide distributor of high-quality housewares since 1938.
According to the company’s website, in the 1970s, Hutzler made the engineering breakthrough that fiberglass can give additional strength that was lacking from traditional nylon. They used this knowledge to produce fiberglas-reinforced nylon utensils, “which are still used today by McDonalds, Burger King and Pizza Hut.”
Company officials did not respond to requests for comment.
Transportation challenges and solutions
While the sight and sounds of big rigs rumbling around the Northwest Corner may annoy some, transportation costs can be expensive and compounded in rural areas where trucks need to make special trips, said Cow-Pots’ Freund.
“There is great value to us, being a small manufacturer in the community, and having the larger companies like BD make a lot of shipping trips, with the trucks coming and going,” she explained. As transportation frequency increases in the area, said Freund, it helps to lower her transportation costs.
CBIA’s DiPentima noted that rural manufacturers struggle with employees’ transportation needs.
“One thing we have heard from the rural manufacturers is that there is not much of it for their employees, especially for what is referred to as the ‘last mile,’ meaning employees can get to a train or bus hub but have challenges getting to their workplace from there.”
Transportation along with housing, child care and cost of health insurance are top issues that CBIA hears from businesses and are at the center of its 2024 legislative policy solutions, said DiPentima.
This article has been updated to reflect the correct name of the PlastiPak syringe and the location of Franklin Lakes, New Jersey.
Charlie Castellanos, left, and Allegra Ferri, right, sitting in the HVRHS library to talk about their experiences in the U.S.
“I would say if you are thinking about doing the program, do it because you get out of your comfort zone and learn so many things...” —Charlie Castellanos
Every year, Housatonic Valley Regional High School welcomes foreign exchange students to attend classes through the AFS Intercultural Programs. This school year, two students traveled to Northwest Connecticut to immerse themselves in American life and culture. Allegra Ferri, a 17-year-old from Italy, and 16-year-old Charlie Castellanos from Colombia sat down to reflect on their experience at HVRHS. As the academic year is coming to an end, they shared a few highlights of their time in the U.S. and offered advice to prospective exchange students.
Allegra: “My favorite part of this exchange year was coming here and experiencing an American high school.”
Charlie: “My favorite part is coming to high school and living the American dream and probably going to ski [for the first time].”
Allegra: “I played volleyball in the fall and I really liked it because everyone was so nice. Then during the winter, I was part of the crew for the musical and now I’m doing tennis. I really enjoy it because it’s a good team. I love how American high school has sports and activities after school.”
Charlie: “I did soccer in the fall, which was my favorite. I did the play in the winter and right now I’m doing track and field. We don’t have school sports in Colombia. This is one of the things I’m going to miss the most.”
Allegra: “I would say do it because living in another country is a great experience to grow and improve another language. It improves your skills of being by yourself.”
Charlie: “I would say if you are thinking about doing the program, do it because you get out of your comfort zone and learn so many things like culture, language and it’s just a completely new experience. It will stay with you your entire life.”
Students from Housatonic Valley Regional High School wrote and produced the inaugural edition of HVRHS Today, a new publication by and for students in the Northwest Corner.
This inaugural issue of HVRHS Today marks the first student-led journalism effort at the high school in several years. The program is a collaboration between the Lakeville Journal, the Berkshire Taconic Community Foundation and the 21st Century Fund.
Anna Gillette, Mia DiRocco, Shanaya Duprey, Madelyn Johnson and Ibby Sadeh volunteered to form the first group of students comprising the staff of the HVRHS Today.
The five girls got to work just before spring break, meeting as a group of reporters for the first time at the Lakeville Journal office in Falls Village on Wednesday, April 9. That night, the team hit the ground running throwing out ideas for their first reporting projects and discussing the basics of gathering news and reporting facts.
In the following weeks, the students gathered weekly every Thursday at the Lakeville Journal office to discuss interviewing, writing and reporting and plan their coverage for the paper. The students took the lead at every turn, choosing which topics they would like to cover and deciding what sources were best for each story.
Anna Gillette, of Lakeville, joined the program out of a passion for research writing and a desire to learn about a potential career path. “I don’t really know what I want to do in the future and I don’t know what career I want to pursue,” Gillette said. “So I think that this is a good opportunity to, kind of, test the waters to see if this is something I would be interested in.”
Gillette contributed reporting on the latest production of the high school’s Unwritten Show, a completely student-led annual production written this year by Sara Huber and co-directed by Huber and Alex Wilbur. Gillette also reported on and profiled the winner of this year’s “Next Top Mountaineer” pageant, a senior named Manny Matsudaira.
Madelyn Johnson, of North Canaan, said she joined the program to hone her writing skills. “My English teacher calls me a ‘stupendously boring writer,’” Johnson said. “There’s not much emotion or anything in my writing. It’s pretty much just fact, fact, fact.” This is a good thing, Johnson said, for Advanced Placement tests, but not necessarily for more creative assignments.
The program pushed Madelyn Johnson out of her comfort zone, something she said her mother has spent her whole life teaching her to appreciate. “My mom has always had me facing my fears,” Johnson said. “Even if I didn’t always like them, I was always sort of forced to try new things. So I’m trying to continue that with the new independence I get as I grow up.”
Johnson profiled the seniors of the HVRHS track team that will be going on to run for their collegiate teams after graduation, and Richie Crane, who won a Sondheim Award for his performance of Old Man Strong in this year’s production of “Urinetown.”
Mia DiRocco, of Cornwall, said she wants to pursue a career in journalism after graduation. “I’m really passionate about politics, and now is a great time for that,” DiRocco said. “And I’m really interested in international relations, linguistics — and I love writing — so, it’s a career that I think encompasses all my interests in one.”
DiRocco focused her reporting on the no-longer-imperiled tennis team and sports involvement at HVRHS in general. Her reporting dug into the benefits of the brand new tennis courts and the efforts required to bring back previously dissolved groups — like the recently reformed cheerleading team.
Ibby Sadeh, of Falls Village, said she expected the program to help her with her social skills. “From the first meeting I definitely thought it could be fun and valuable to learn new skills and build on my social skills,” Sadeh said. “And also help with my writing skills. I’ve only done essays and reflections for class. I haven’t actually written in this form before.”
Sadeh contributed the inaugural reporter’s notebook report, reflecting on this year’s trip to Europe. Sadeh also worked with DiRocco to recap the first year behind the scenes with the Bias Education and Response Team, and with Gillette to produce a Q&A with this year’s foreign exchange students — 17-year-old Allegra Ferri from Italy and 16-year-old Charlie Castellanos from Colombia.
Shanaya Duprey, of North Canaan, like many of her compatriots in the program, wanted to seize an opportunity to improve her writing, but for a career in marine biology. “I’ve always been really interested in animals,” Duprey said. “I’ve found a new passion for the ocean. There’s not a lot of attention on marine conservation so I’d like to do that.” Duprey said style of researched, journalistic work she produced for HVRHS Today could help her in a future career as a scientist writing and submitting grant proposals and research papers.
Duprey focused her reporting over the past six weeks on the 21st Century Fund, a nonprofit organization that provides funding for educational opportunities and scholarships to HVRHS students. Her reporting focused on Silas Tripp, a student at HVRHS that could attend multiple educational engineering camps thanks to money from the 21st Century Fund.
HVRHS Today can be found online at www.lakevillejournal.com/hvrhs-today.
WATERTOWN — Housatonic Valley Regional High School girls lacrosse played Watertown High School for the Western Connecticut Lacrosse Conference championship Wednesday, May 28.
The cold, rainy game went back and forth with three ties and three lead changes. Watertown was ahead when it counted and earned a 6-4 victory to claim the league title.
Under the lights in Watertown, both sides displayed defensive discipline in a hard-fought match. It was the third meeting between these two teams this season and Watertown completed the sweep in the title game.
Watertown scored first in the opening minute. Housatonic quickly evened the score when freshman Annabelle Carden tucked a shot past the goalie on a fast break. The first quarter ended 1-1.
Freshman Annabelle Carden, no. 9, scored the first two goals for HVRHS in the title game May 28.Photo by Riley Klein
HVRHS pulled ahead with another goal from Carden in the second quarter. A few minutes before half time, Watertown tied it up again at 2-2 going into intermission.
Watertown regained the lead in the second half before HVRHS answered with a goal by senior Tessa Dekker. With seconds left in the third quarter, the Warriors went up 4-3.
As the sky darkened and rain intensified in the fourth quarter, Watertown built a lead. They scored twice in a row to start the final period and entered clock-management mode to drain time. Senior Lola Clayton scored once more before time was out and the game ended 6-4.
Housatonic's defense held Watertown to six points in the championship game. Watertown, the number one team in the WCLC, averaged more than 12 goals per game this season.Photo by Riley Klein
The championship’s most valuable player award went to Malia Arline of Watertown. HVRHS had five players chosen to the 2025 all-league team: Lola Clayton, Lou Haemmerle, Mollie Ford, Neve Kline and Georgie Clayton.
“Incredible finals. Incredible game to watch,” said HVRHS Coach Laura Bushey to her team post-game. “You should all be very proud of yourselves.”
“Holding a team to six points is something to be really, really proud of. Especially a team that’s as good as these guys,” said assistant coach Erin Bushey.
HVRHS qualified for the Connecticut Interscholastic Athletic Conference Class S lacrosse tournament. The Mountaineers got matched against Wolcott High School in round one May 30. HVRHS won 13-6 and advanced to the second round to play top ranked Lauralton Hall June 3 in Milford.
Lou Haemmerle created offensive opportunities for HVRHS in the league final.Photo by Riley Klein
“Some I prefer are the grilled cheese. Pizza’s okay with some sauce. Hamburger too, I guess. The least favorite that I’ve tried is probably the hot ham and cheese. I don’t like that. I’ve started to see that they’re doing French fries, which I kind of like. They should probably start doing more of that.”
“My favorite lunch is probably the mac and cheese and popcorn chicken. I’d like to see it more frequently. Grilled cheese, cheese quesadilla, french toasts sticks, and chicken fajita
can all go.”
“My favorite is beef nacho grande. My least favorite is probably the fajitas.
I wish we had chicken nuggets and mashed potatoes more often.”
“General Tsou’s chicken is my favorite lunch. Also, the popcorn chicken and mac and cheese.
I really don’t like the French toast sticks or that we have pizza every Friday. We need some more variation.”
Photos by Ibby Sadeh and Mia DiRocco